Supply Planning & Inventory Management
Effective supply planning and inventory management ensure product availability while minimizing costs. The key is aligning supply with forecasted demand and optimizing stock levels. Below are essential strategies to manage inventory efficiently.
Supply Planning: Aligning Supply with Forecasted Demand
Supply planning ensures that the right products are available at the right time. This involves:
- Demand Forecasting: Leveraging historical data, market trends, and predictive analytics to estimate future demand.
- Capacity Planning: Aligning production and supplier capacity with forecasted needs.
- Supply Chain Coordination: Collaborating with suppliers and logistics partners to prevent shortages or overstocking.
Inventory Management Strategies
Effective inventory management prevents excess costs and stockouts. Here are four key strategies:
1. Safety Stock (Buffer for Demand Spikes)
Safety stock acts as a cushion against unexpected demand surges or supply chain disruptions.
- Required safety stock depends on demand variability, lead times, and service level targets.
- Formula:

Where:
- Z = Service level factor (based on desired probability of avoiding stockouts)
- σd = Standard deviation of demand
- L = Lead time in days
2. Reorder Point (ROP) Calculation
The reorder point indicates when to place a new order before stock runs out.
- Formula:

- Example: If daily demand is 50 units, the lead time is 10 days, and the safety stock is 200 units:
- ROP = (50 x 10) + 200 = 700
An order should be placed when inventory drops to 700 units.
3. Economic Order Quantity (EOQ) (Balancing Order Costs vs. Holding Costs)
EOQ determines the optimal order quantity to minimize total inventory costs.
- Formula:
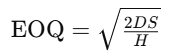
- D = Annual demand
- S = Ordering cost per order
- H = Holding cost per unit per year
- Example: If annual demand is 10,000 units, order cost is $50, and holding cost is $2 per unit:

The company should order 707 units per cycle to optimize costs.
4. ABC Analysis (Prioritizing Inventory Based on Importance)
ABC analysis classifies inventory items based on value and business impact:
- A Items: High-value, low-quantity items requiring strict control (e.g., expensive machinery parts).
- B Items: Moderate-value items with moderate control.
- C Items: Low-value, high-quantity items requiring minimal oversight (e.g., office supplies).
This helps focus resources on high-impact items while reducing efforts on lower-value stock.
Conclusion
Supply planning and inventory management are crucial for ensuring product availability while controlling costs. By implementing safety stock, reorder points, EOQ, and ABC analysis, businesses can optimize inventory levels, reduce waste, and improve service levels. A well-structured approach strengthens the supply chain and enhances profitability.
Want to dive deeper into supply chain insights? Sign up for our newsletter and get clear, actionable articles delivered straight to your inbox—no spam, just valuable tips to boost your forecasting and supply chain strategies.